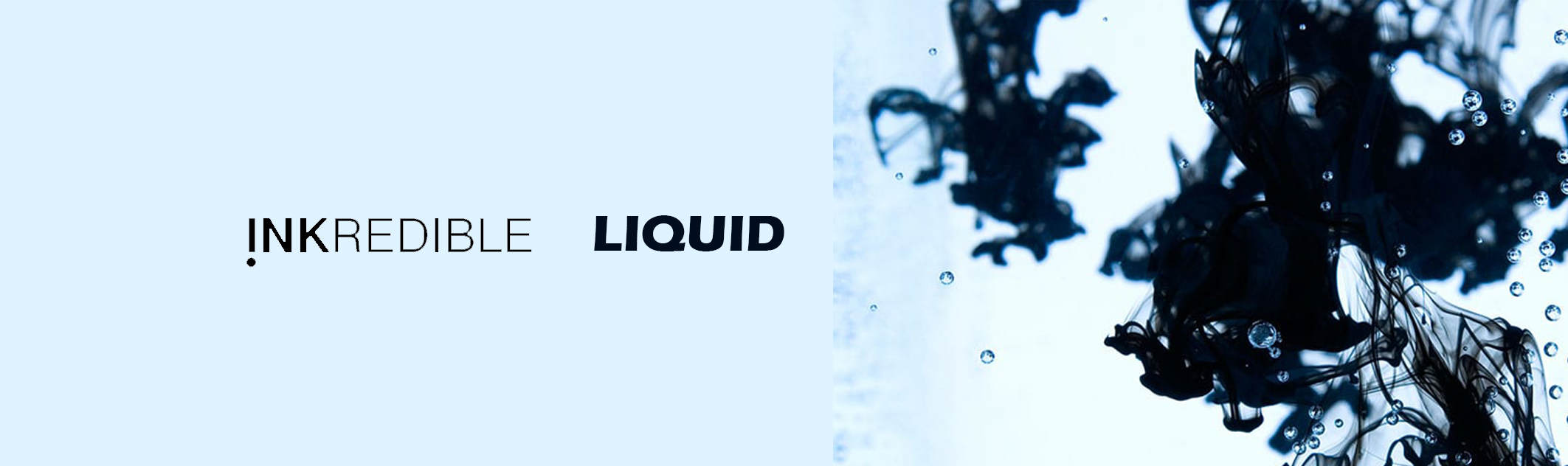
Solvent based LIQUID Inks
Gecko Xtreme and Gecko Bond Star are whites especially dedicated to high performance lamination (please refer to the respective Technical Data Sheets). Due to the exceptional performances in respect to bonding values, opacity and solvent retention, their use is more and more extended to applications printed over the standard use with Gecko Bond Star colored inks as well as applications where Gecko Bond Top are used. The final results, of course, are strongly affected not only by the characteristics of these products, but also by the quality of the primary and secondary films used (consistency of the surface energy in case of corona treated films, quality of the coating in case of chemical treated ones), quantity of ink applied, quality and quantity of adhesive applied, solvent retention, converting set up and post- Gecko Bond Star 06/2022 Page 2/3 lamination treatment of the laminate. Using some solvent-less adhesives normally related to general purpose and high speed applications, a penetration of the adhesive into the white layer has been noticed by an initial aesthetic effect. This is caused by the low molecular weight of PU used in these adhesives. Normally, in case of proper converting application, this effect disappears when curing of the adhesive is completed. In case of Gecko Bond Star white this phenomena can be strongly reduced adding 1 – 2 % of 70GH278345 Adhesion promoter. The customer nevertheless has to apply a preliminary test in order to fully evaluate the effect of this addition in terms of the final bonding values and light fastness. Our Technical Support team is available for any further suggestion. Metallics A full range of GeckoÒ imitation gold and silver inks is available. Additives It is available a PET/PA additive (70GH325253, addition 2 – 3 %), which allows to increase bonding performance on some substrates. Please refer to your local technical service to verify the possible applications. Gecko® Bond Star will not reach immediate tape test adhesion when printing directly on BOPP or coex OPP. An adhesion promoter (70GH278345) is available in order to improve initial adhesion (use at 3%). Process Inks A range of slow drying flexo half-tone process colours is available (GBS raster).
Instructions for the use of printing inks for the production of primary food packaging For information on the use of printing inks, varnishes and additives for the manufacture of food packaging please refer to the respective „Statement of Composition”. This information is provided to allow the calculation of possible levels of migration of evaluated substances in a worst case situation. Migration tests at hubergroup laboratories with printed samples made from commercially available OPP film (film thickness: 35 u. printed wet ink: 6 g/m2 , with 95 % ethanol as the food simulant) and PE film (film thickness: 50 u, printed wet ink: 6 g/m2 , with 95 % ethanol as the food simulant) showed no migration of substances above legal limits. Based on the results of these migration tests, we expect that the printed inks enable the final printed products to comply with the legal requirements for packaging for all kinds of foodstuff. The manufacturer of the finished article and the filler have the legal responsibility to prove by appropriate migration testing that it is fit for its intended purpose. In order to maintain low residual solvents concentration in the printed film, the printer must ensure sufficient drying of the product, especially when retarders have been added. Residual solvent content must be regularly monitored. The products must not be used in the manufacture of packaging where the printed ink layer is intended to come into contact with foodstuff (direct food contact). There are restrictions for the use of printing inks for applications where temperatures above 100 °C for extended periods of time are applied. For details, please see document “Food Packaging Inks for High Temperature Applications”. Health & Safety The material safety data sheets contain all relevant information for the generation of appropriate internal plant instructions. The user is responsible for all local legislation requirements. Ink Handling Please refer to General Guidelines for handling inks for flexible packaging. Storage Conditions Store the material in the original packaging at a temperature not below 5°C and not in direct contact with sunlight.
Grouping LIQUID Inks
There’s a science behind your choice of ink. Different flexo printing inks are crafted to work best with varying image carriers and substrates.
There are a few considerations that go into this:
One of the most important of these is surface tension. Inks naturally want to flow to the higher dyne level. Proper surface tension configuration allows the most ink possible to be transferred to the substrate and ensures a full and even wet out.
Other considerations include:
- Chemical compatibility
- Final product usage
- Print speed requirements
- Regulatory compliance
- And others
Choice of substrate is also one of the main factors in ink selection.
Substrates can include:
- Corrugated board
- Paper
- Laminates
- Film
- Foils
4 Common Types of Flexographic Inks
- Water based
- Solvent based
- Ultraviolet and electron beam
- Oil based
Here are some more details on these types of inks, and what applications they’re best for:
- WATER BASED
- Composed mainly of water and pigment with assorted additives like defoamers and agents to aid in drying and adhesion
- Generally have the highest surface tension of all ink types
- Good for any elastomer type, but natural blends are most common
- Popular in the corrugated packaging industry
- SOLVENT BASED
- Composed mainly of alcohols, acetates, and pigments with 80-90% of alcohols and 10-20% of acetates being common starting ratios
- Usually have much lower surface tensions than water-based
- EPDM elastomer is recommended
- Popular for plastic shopping bags and industrial films
- ULTRAVIOLET (UV) AND ELECTRON BEAM (EB)
- Composed of prepolymers, monomers, photoinitiators, and pigments.
- Dries and adheres only when exposed to UV light or electron beam.
- Higher viscosity
- EPDM elastomer is usually recommended for its resistance to ozone
- Popular in the outer-wrap food packaging industry
Have questions on basic Flexographic topics? Check out our new Flexo 101 resource hub below:
- OIL BASED
- Composed of hydrocarbons and pigments and sometimes soy oil
- Solvents blended are very harsh, such as naphtha and hexane
- Mineral oil is sometimes used
- Buna/nitrile elastomer is recommended
- Popular in the publication printing industry
Flexographic inks are separated into two classifications: volatile and energy curable.
- Volatile inkscontain a liquid solvent — like water or alcohol — that evaporates and leaves the image on the substrate.
- Energy curable inksdry through intermolecular bonding, which solidifies the ink on the substrate.
Choosing Between Flexographic Inks
Any ink — in the right formulas — could work on nearly any substrate. But some physical combinations work better together, such as solvent based on plastic bags or oil based on newsprint.
Surface tension is a primary consideration in this choice. The ink should be the lowest dyne level. The printing surface of the plate or sleeve should be a higher dyne level, and the substrate the highest. Again, inks are drawn toward the higher surface energy.
ICYMI: We have a full guide to surface tension, and dyne level considerations for optimum printing.
Water-based inks typically face limitations on press speeds. However, solvent-based inks are known to dry in conventional ovens at high press speeds.
If the substrate is absorbent:
- Drying both water- and solvent-based inks is generally similar
- Water based is most commonly used
If the substrate is non-absorbent:
- Ability to dry the ink is critical
- Printers typically choose solvent-based, or UV curable inks
- Some water-based formulas do work
Good substrate and ink suppliers will work with printers to identify the best materials for a final products graphic, physical, and even chemical requirements.